All our services
We offer a lot of services to solve your problems. Here you can find what those services are.
We help you making the changes in your organisation that have a lasting impact.
Learn more →Human resources and staffing solutions to improve everything regarding hiring and optimising your staff.
Learn more →Confused? Take the quiz and we will show you the services that might present a solution to your problem.
Take the quizCommunication workshop
Learn ways of effective communication to foster understanding and improving team work. Learn More →BRL 9320 Implementation
Comply with laws and regulations for producing asphalt Learn More →Vessel Management Support
Ensuring compliance with vessel management requirements Learn More →Vessel Management Internal Audit
Ensuring compliance, cost reduction, and a safer environment Learn More →Take your business processes to the next level!
With our tailor-made platform, you can bring all business processes together in one platform.
Impactive is the platform to enhance your organisation’s quality, safety, health, and environment.
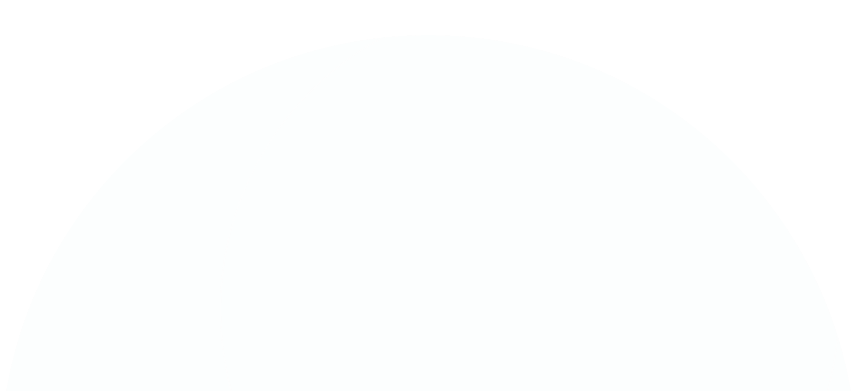
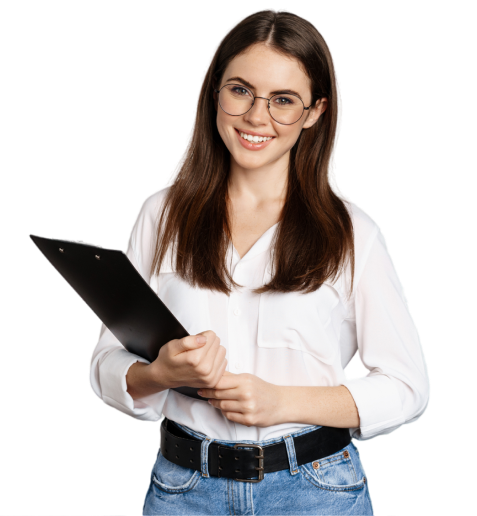